- Home
- Daily Field Report Report ID: 60925
- This project is inactive from admin.Download Report
Daily Field Report
Observations/Finding
Representatives Present:
- Avinash Bandam (ASEC)
- Josh Kelly (Jackson Demolition)
Purpose of Visit: The site visit was conducted at the request of Jackson Demolition’s representative, Josh Kelly, to monitor, verify, and document the ongoing project activities. The objective of the visit was to ensure that all construction and engineering activities are in alignment with established standards and procedures.
Observations:
- Fill Material Placement:
- Approximately 2,466 cubic yards of fill materials were placed for Lift 31 in two distinct sections: Section 1 basement area B7 (Reference: E720661 S1-R8) and Section 2 part 1 basement area G7 (Reference: E720659 S1-R8).
- The placement and compaction of the fill materials were conducted in general accordance with the guidelines outlined in ITP-001.
- The designated fill area is highlighted in brown on the attached drawing.
- Testing and Verification:
- Moisture density testing was performed using a nuclear gauge to assess the moisture content and density of the materials in the basement area.
- Probing was carried out on the placed fill to verify the compaction of the lift. This step ensures that the materials have been properly compacted and meet the required density standards.
- A check-plug test was conducted to verify the Proctor curve intended for use. This comparison ensures that the compaction achieved aligns with the specified Proctor curve.
- The specific test locations are clearly marked on the enclosed drawing.
- HDPE Pipe Installation:
- Around the HDPE pipe, which functions as a dewatering well located at the southeast corner, aggregate was carefully placed. This serves to facilitate dewatering operations.
- Subsequently, the aggregate was wrapped with geo-fabric to prevent the migration of fines. This step aligns with the measures specified in ITP-003, aimed at maintaining the integrity of the dewatering system.
Conclusion: The site visit confirmed that ongoing construction activities are generally in accordance with established standards and procedures. The use of a nuclear gauge for moisture density testing, probing of placed fill materials, check-plug testing for verifying the Proctor curve, and the meticulous installation of the HDPE pipe with associated dewatering measures demonstrate a comprehensive approach to quality control. The installation of the HDPE pipe with geo-fabric further adds to the overall compliance with project specifications.
Recommendations: Based on the observations made during the visit, no immediate recommendations or corrective actions are required at this stage. However, it is advisable to maintain the current level of vigilance in monitoring construction progress and conducting regular quality checks to uphold the high standards demonstrated during the visit.
For any further inquiries or clarifications, please feel free to contact us and we will be more than happy to discuss it with you.
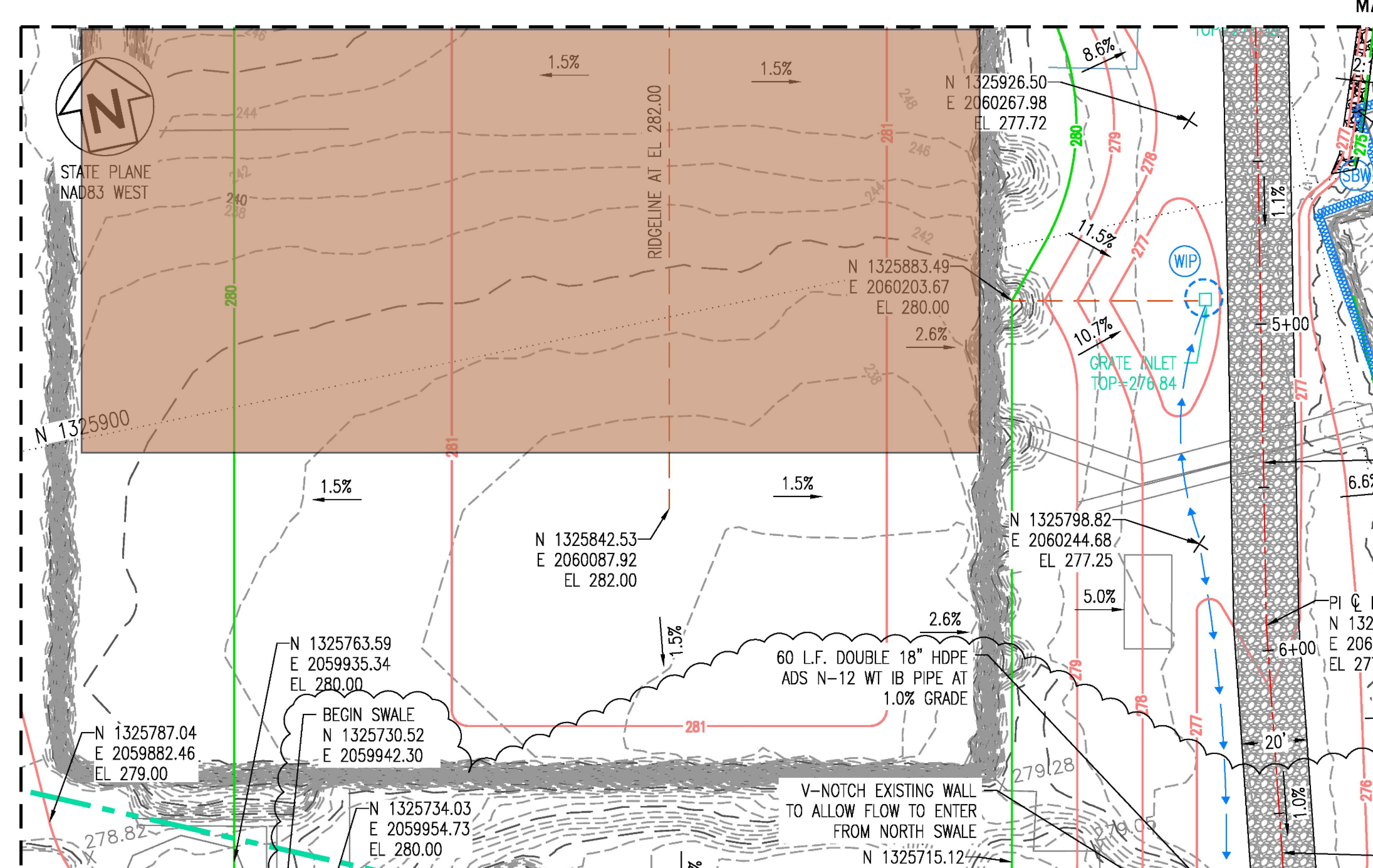
Highlighted region depicts the placement of fill materials in section 2 part 1
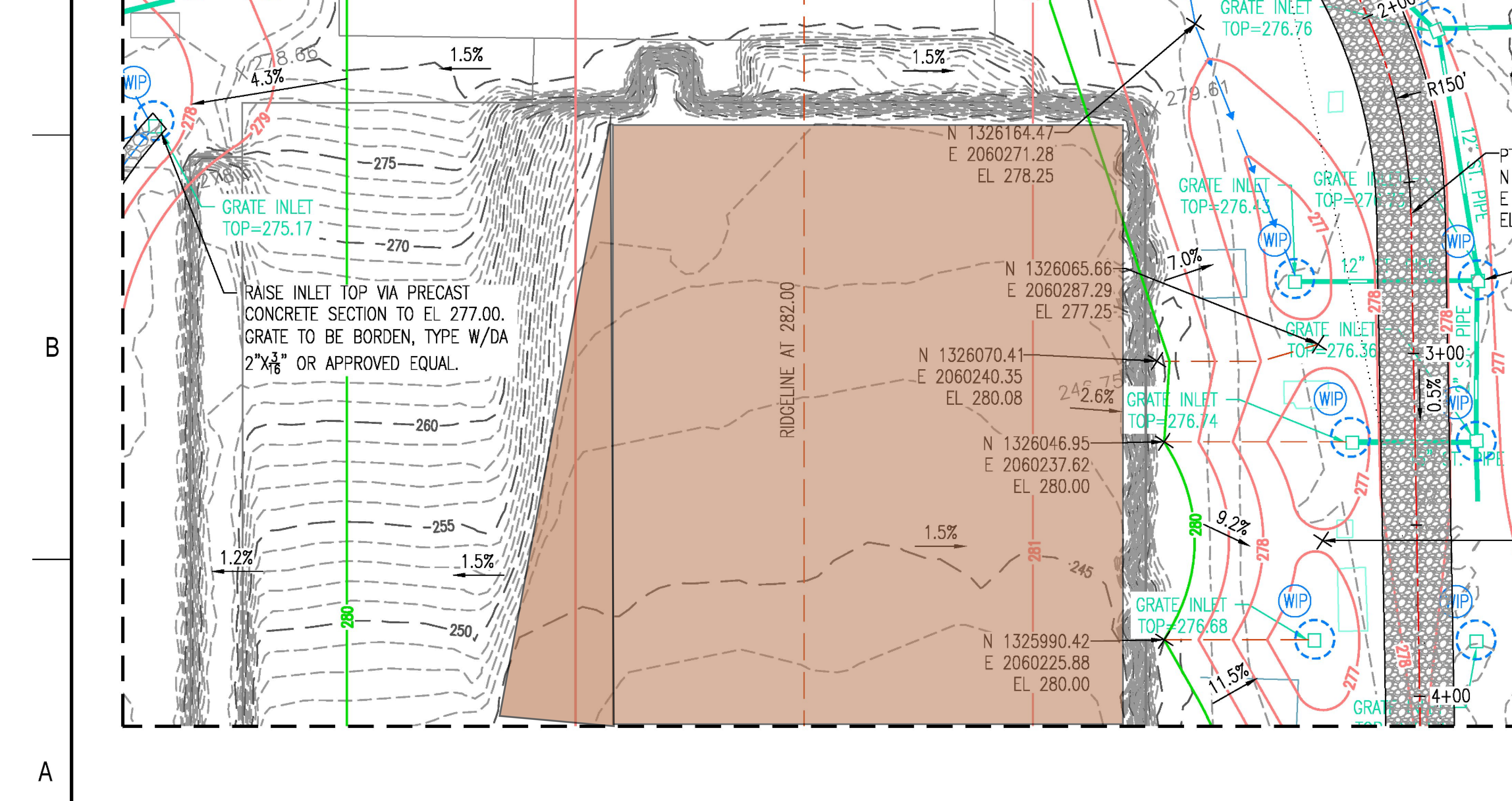
The highlighted region depicts the placement of fill materials in section 1
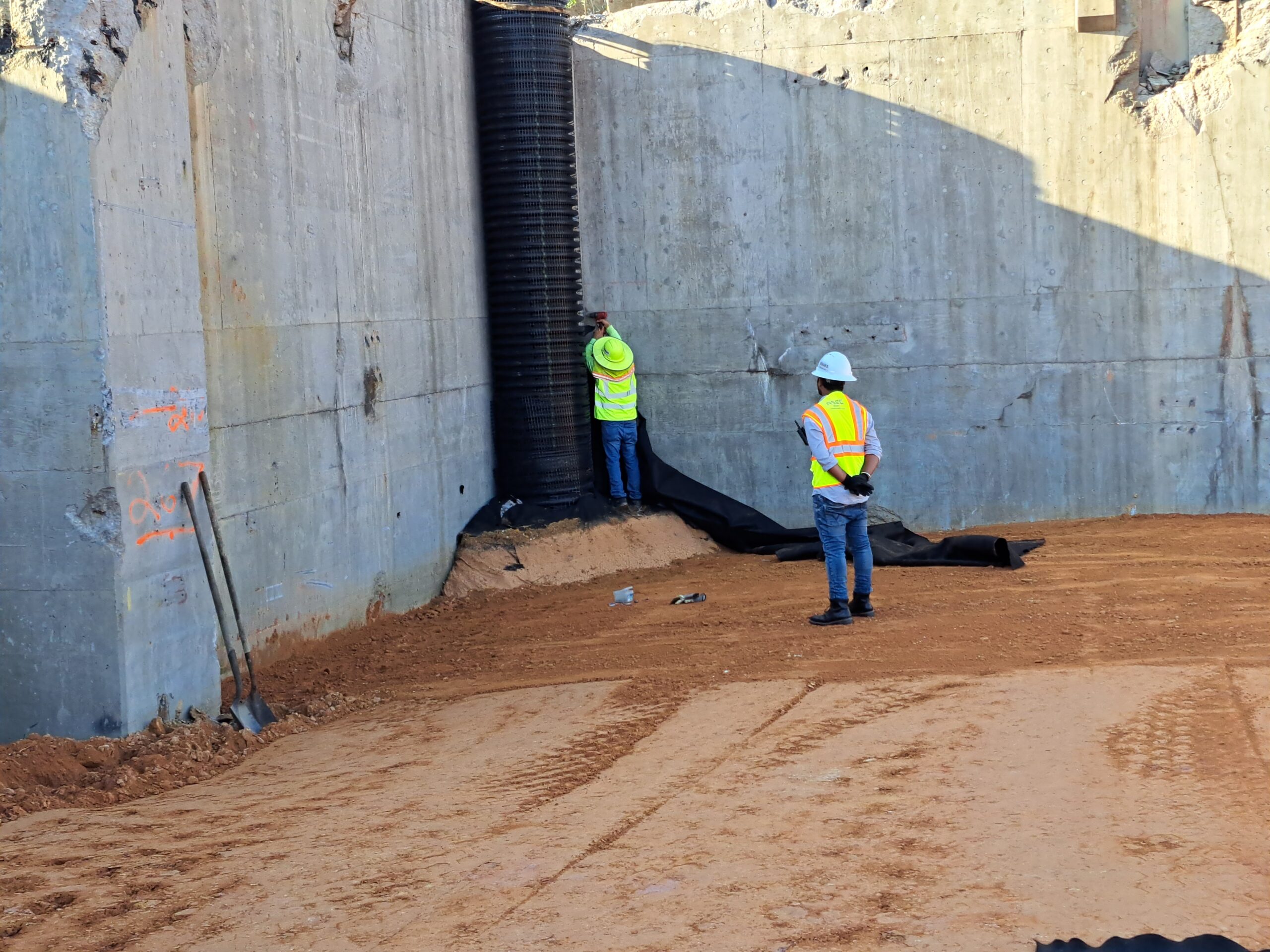
Placement of geo-fabric around HDPE pipe
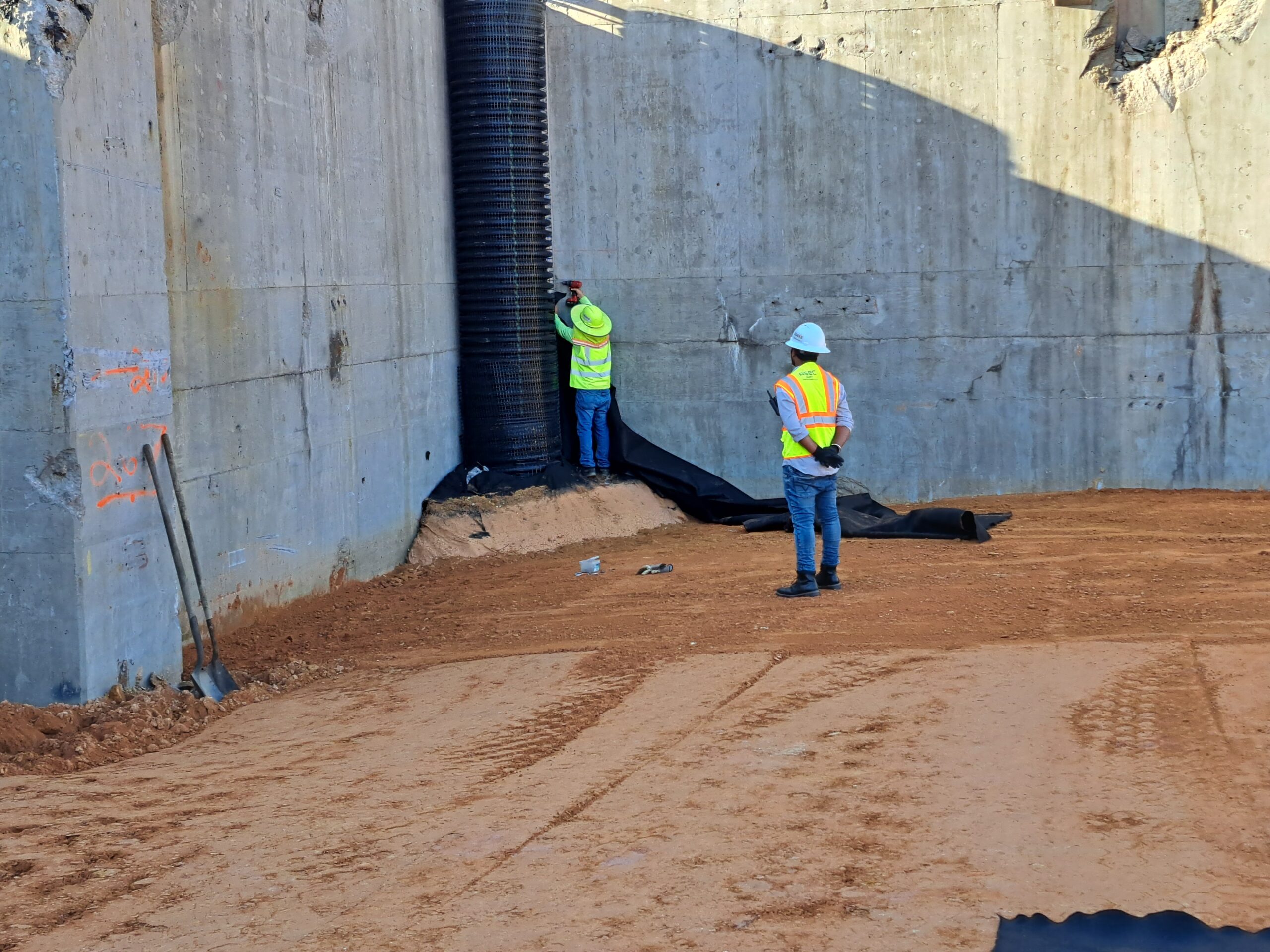
Placement of geo-fabric around HDPE pipe
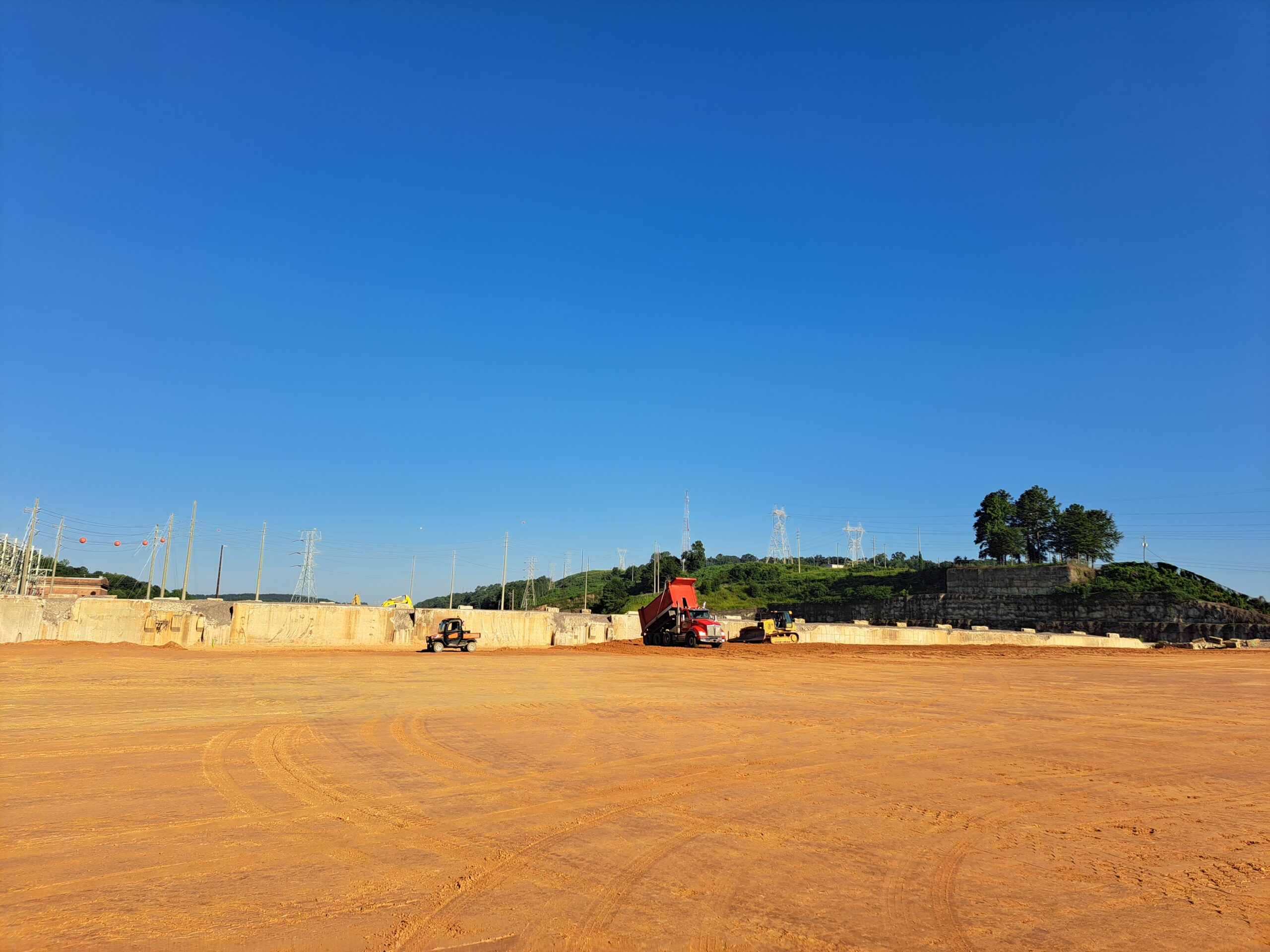
Started the new lift in section 1
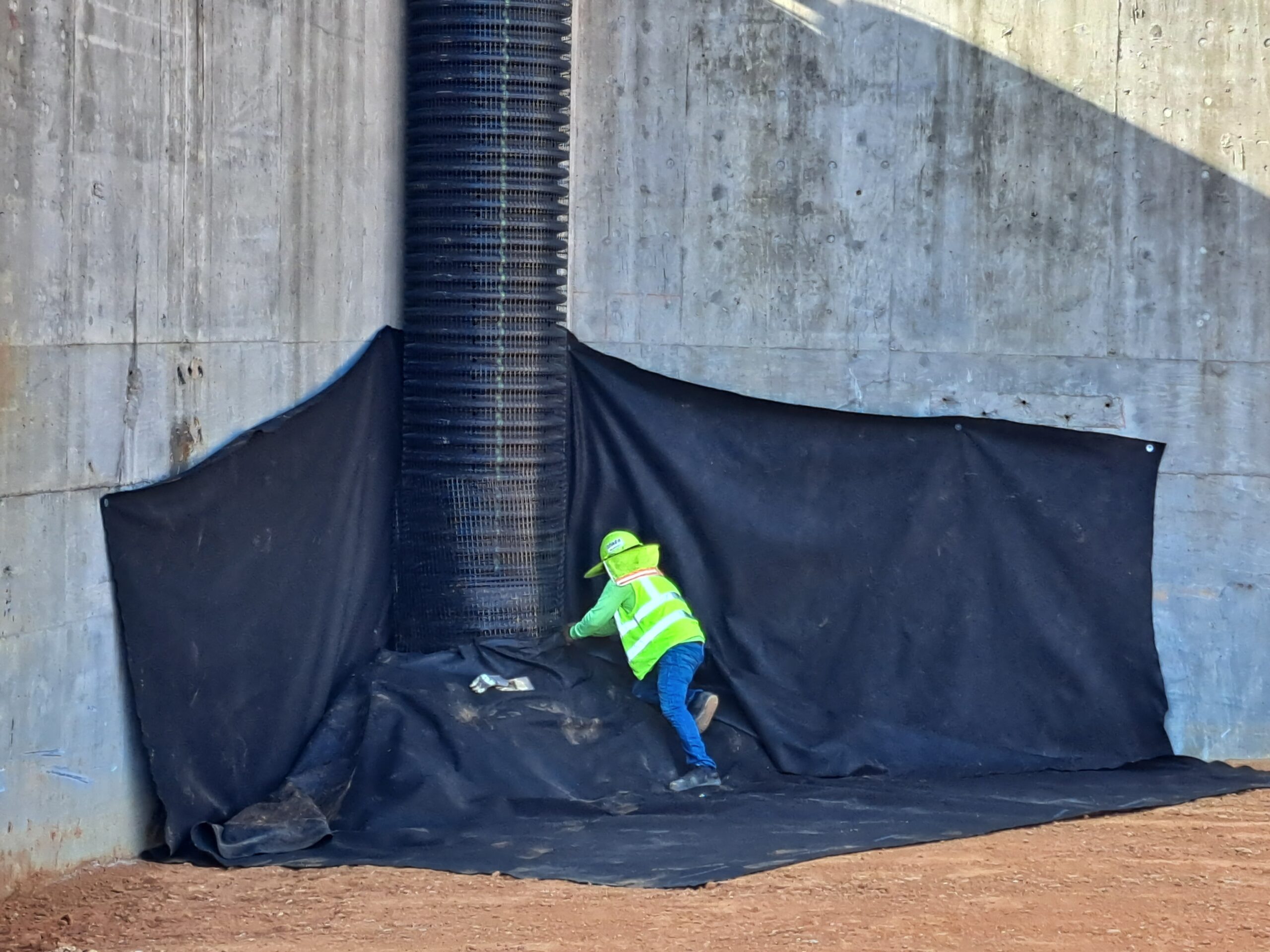
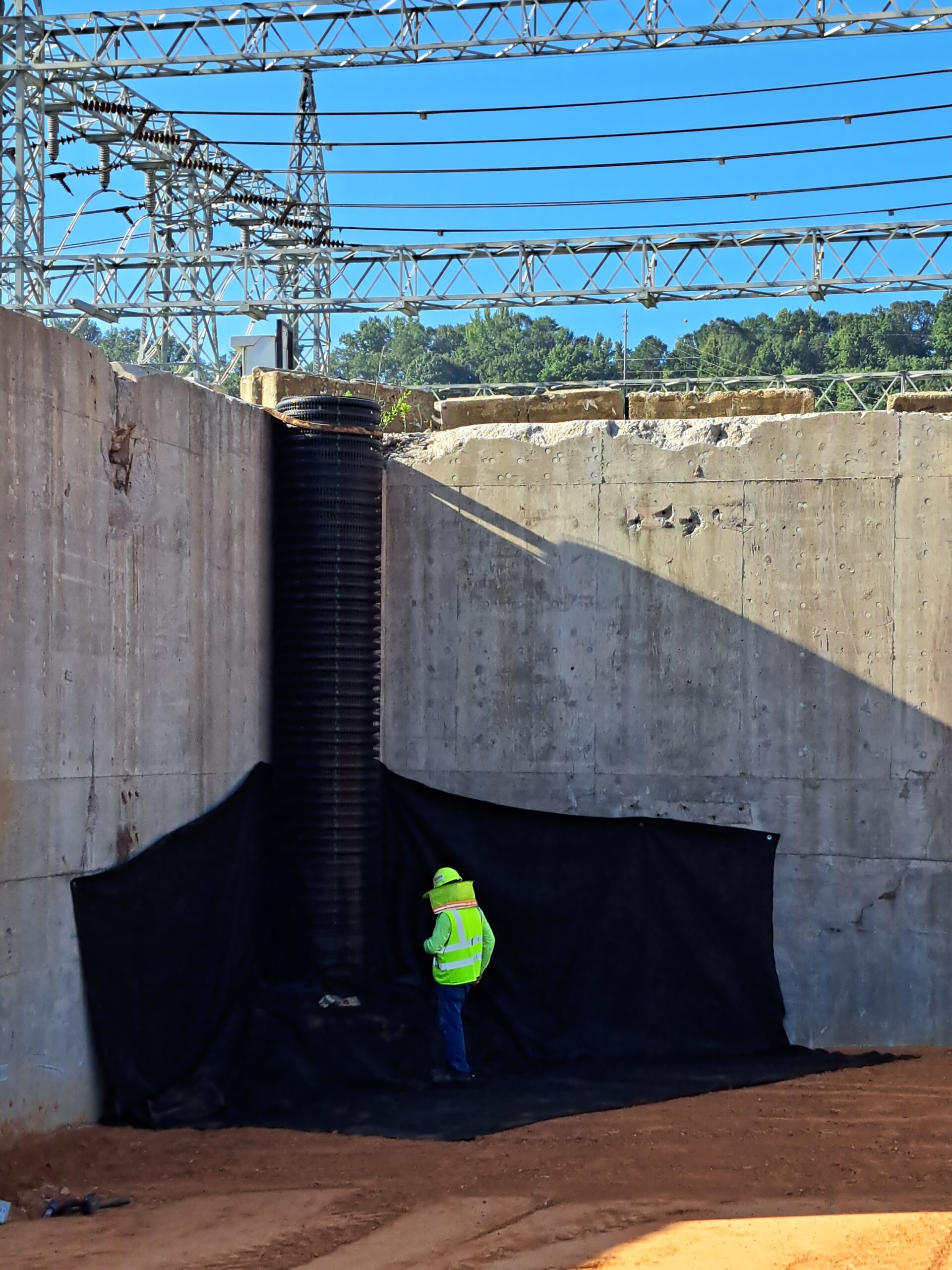
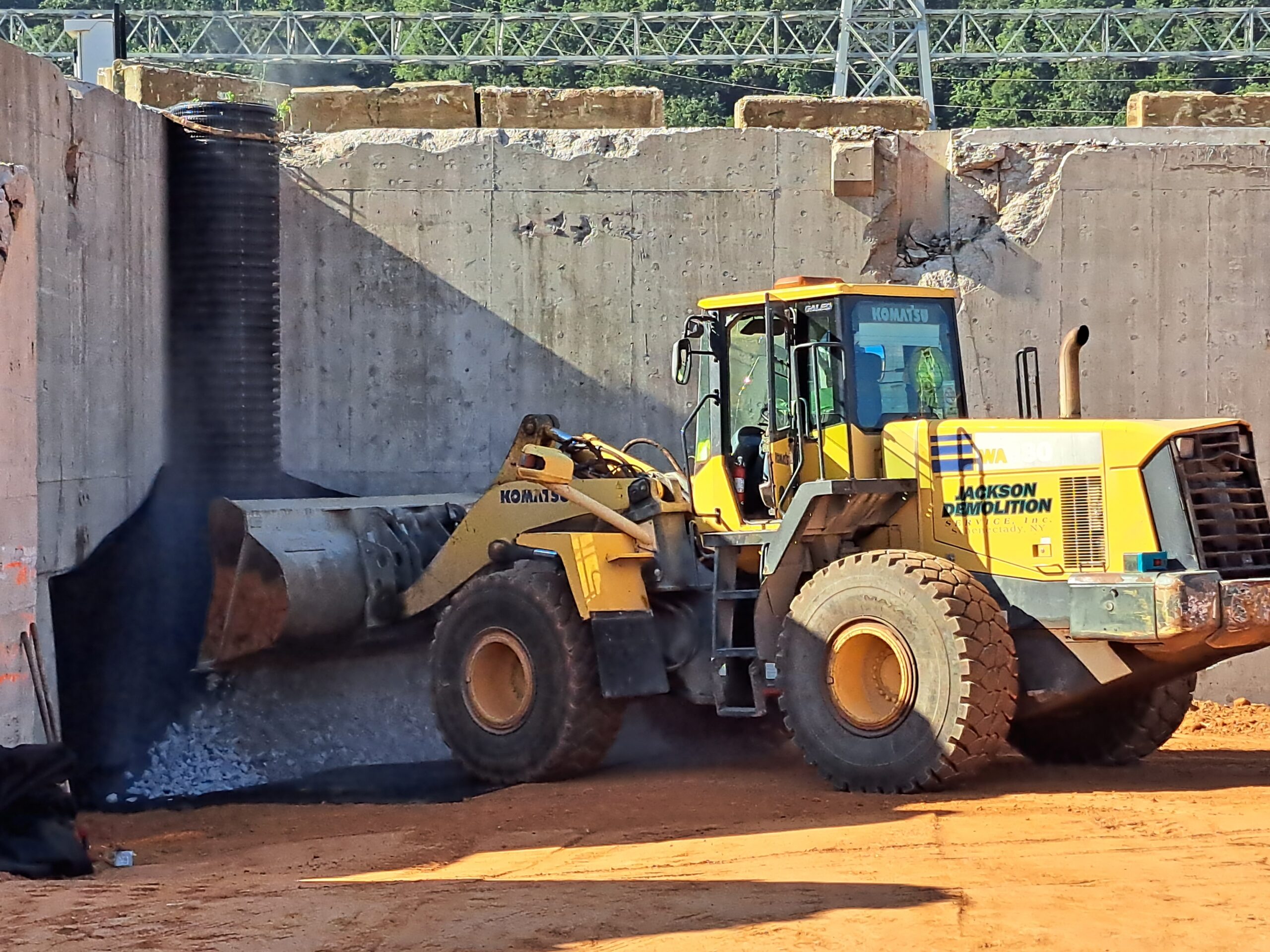
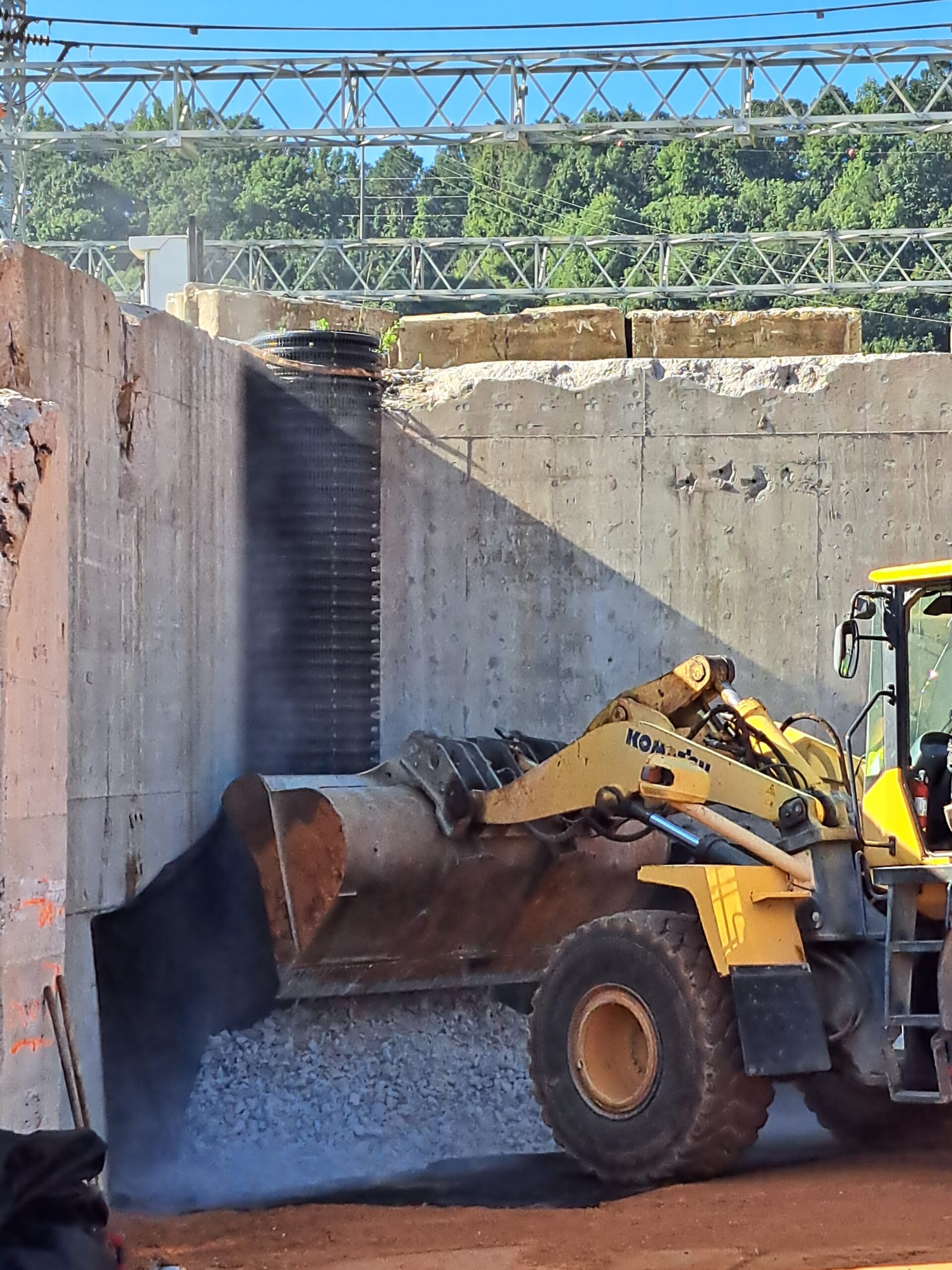
Placement of stone aggregate around the HDPE before the coverage of geo-fabric
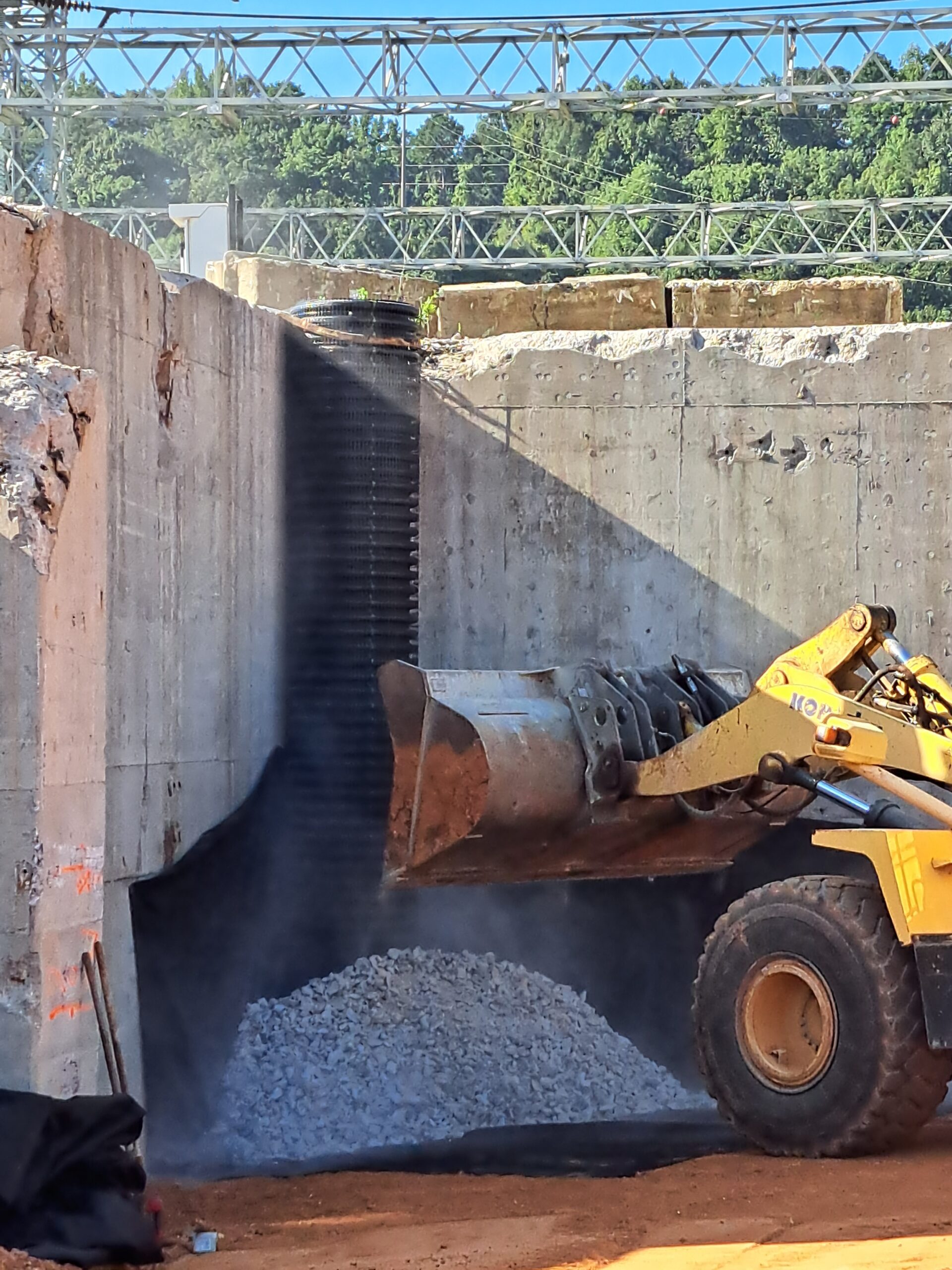
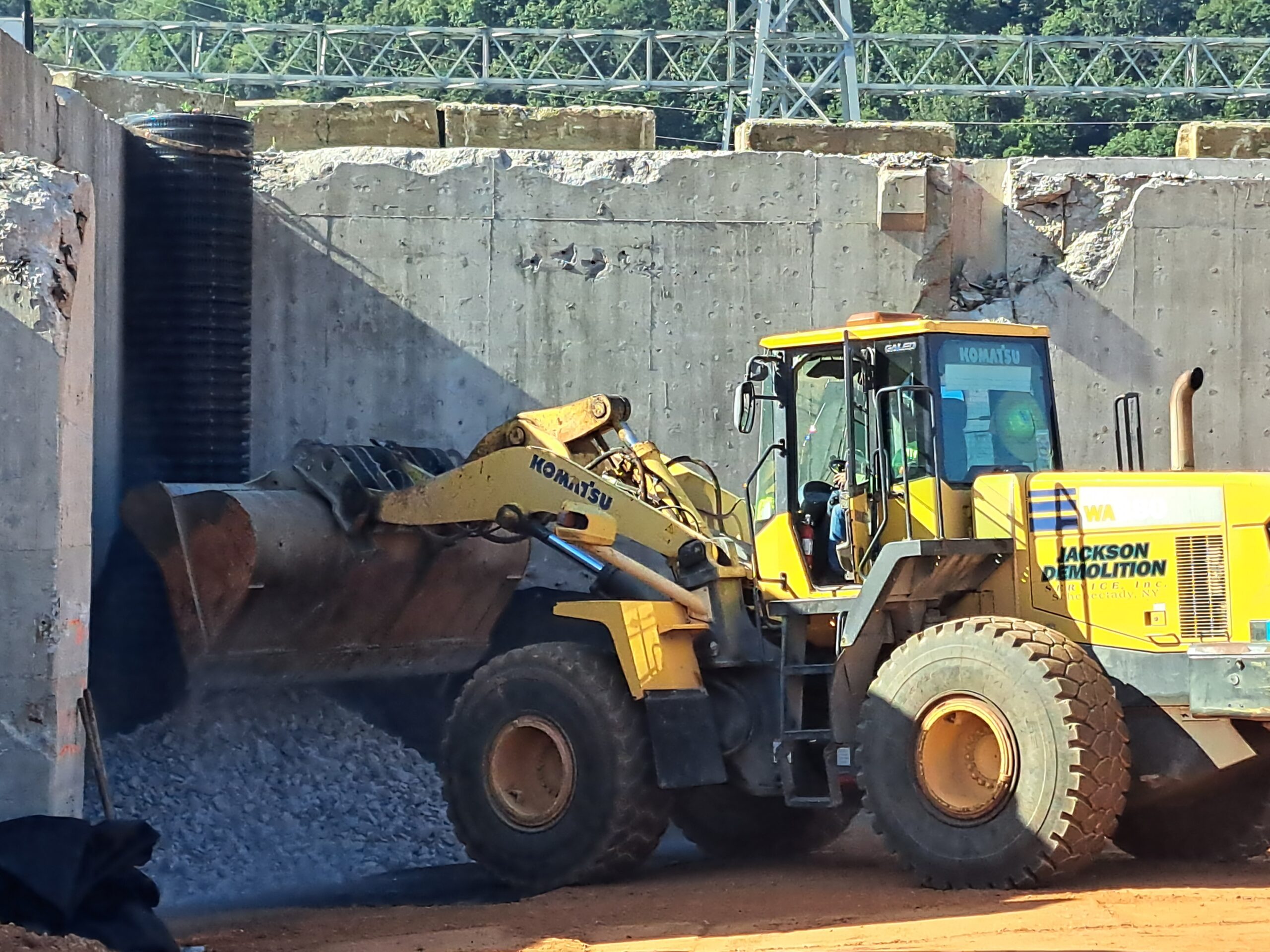
Placement of stone aggregate around the HDPE before the coverage of geo-fabric
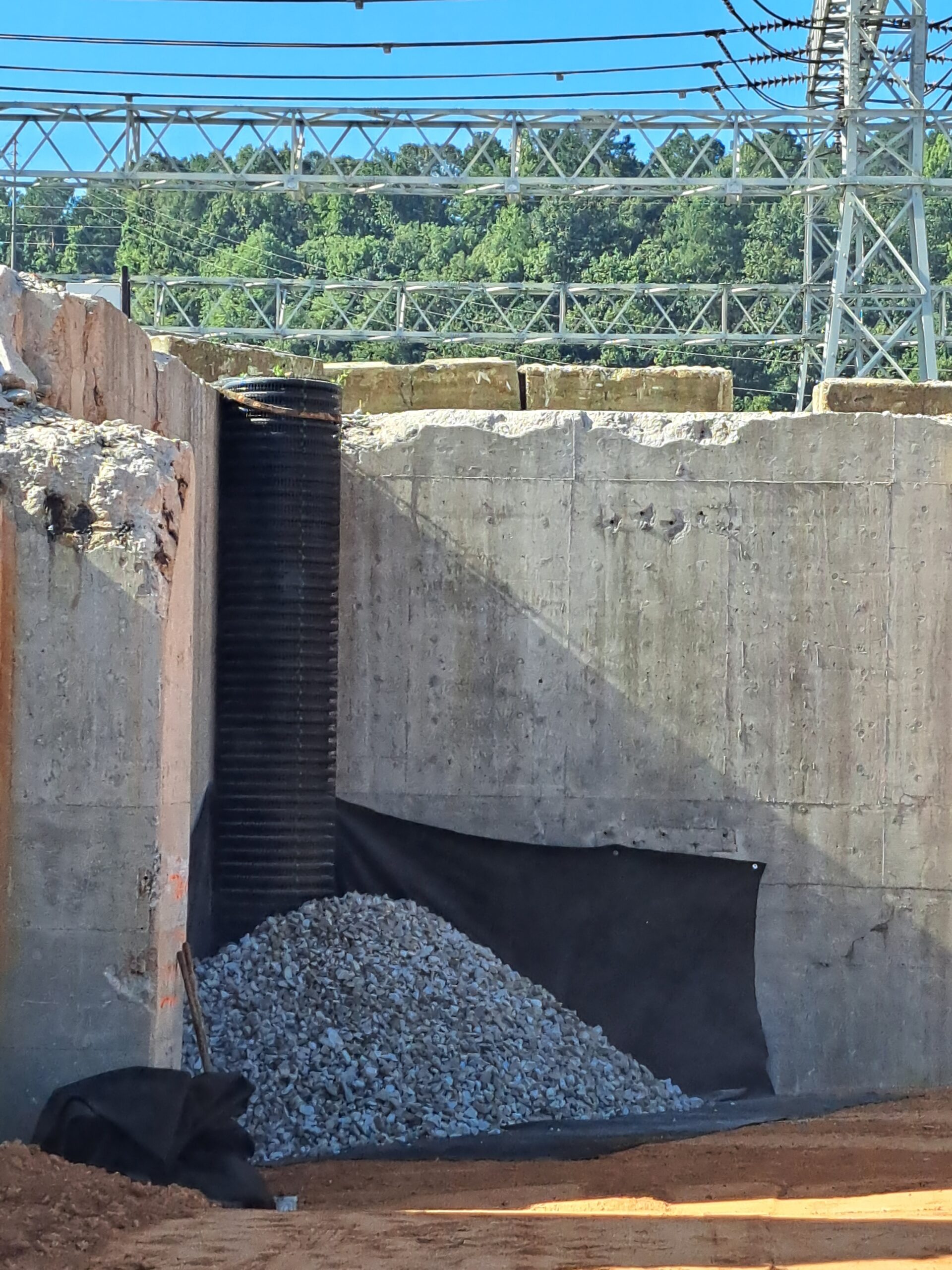
Placement of stone aggregate around the HDPE before the coverage of geo-fabric
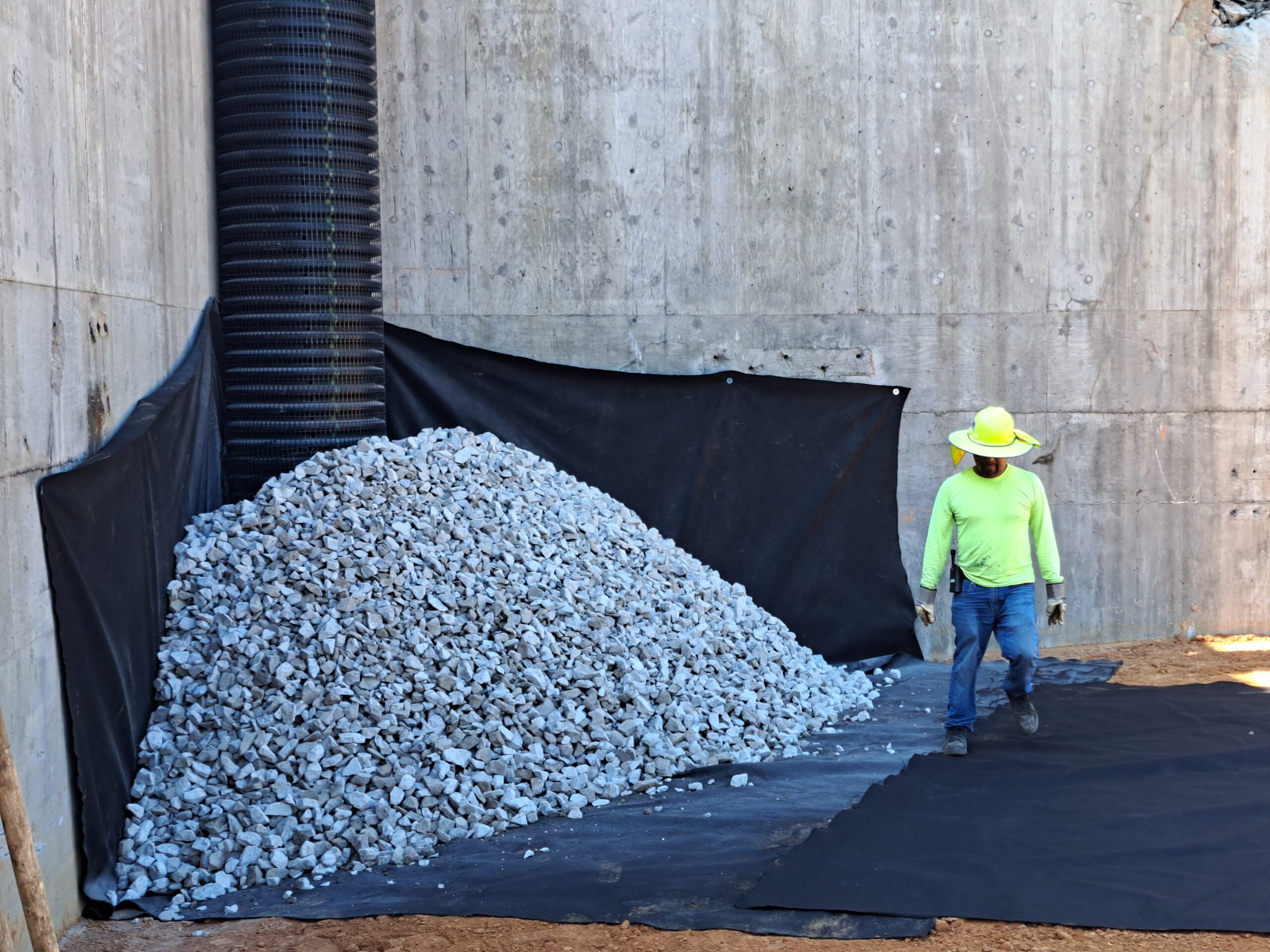
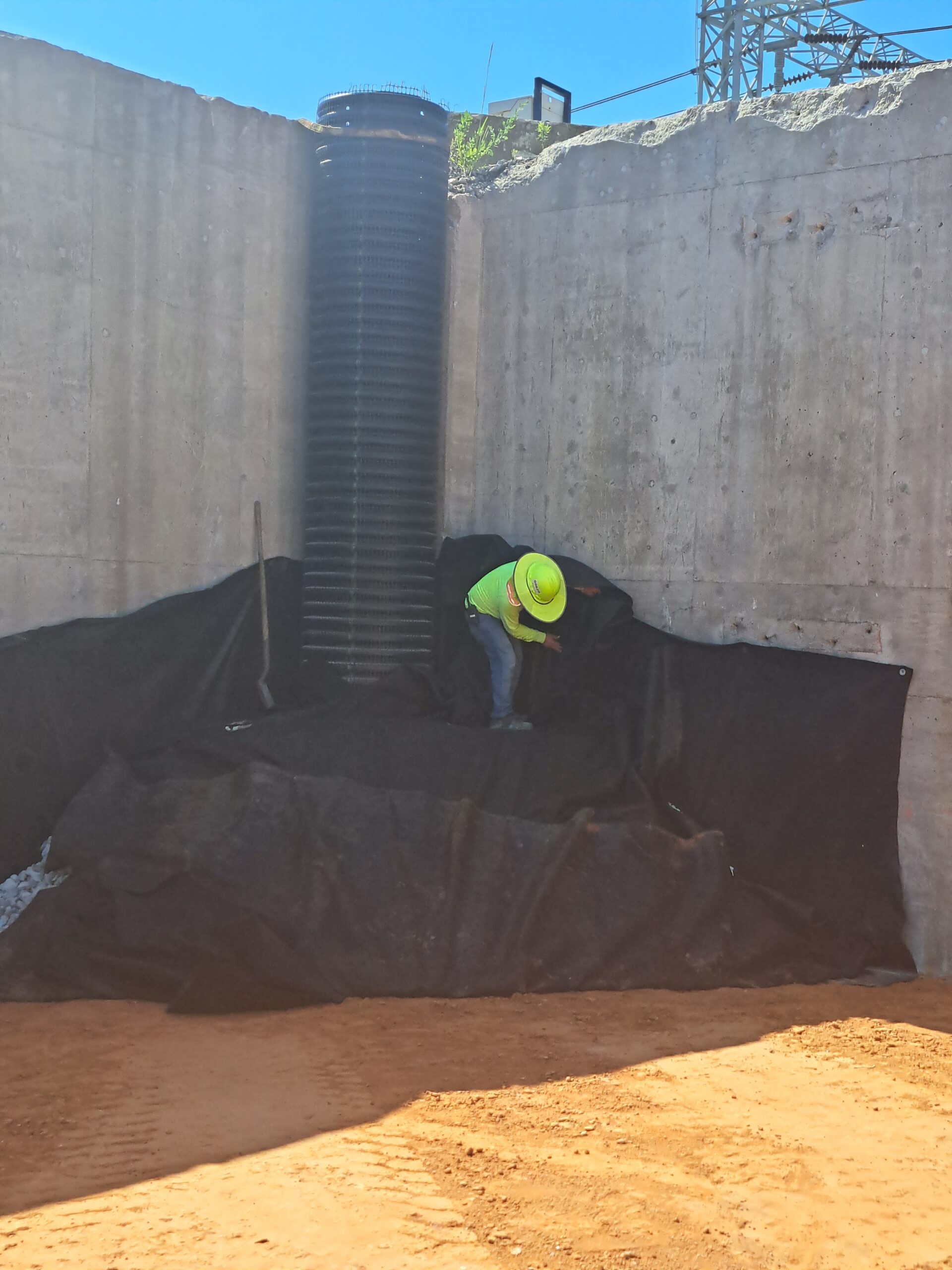
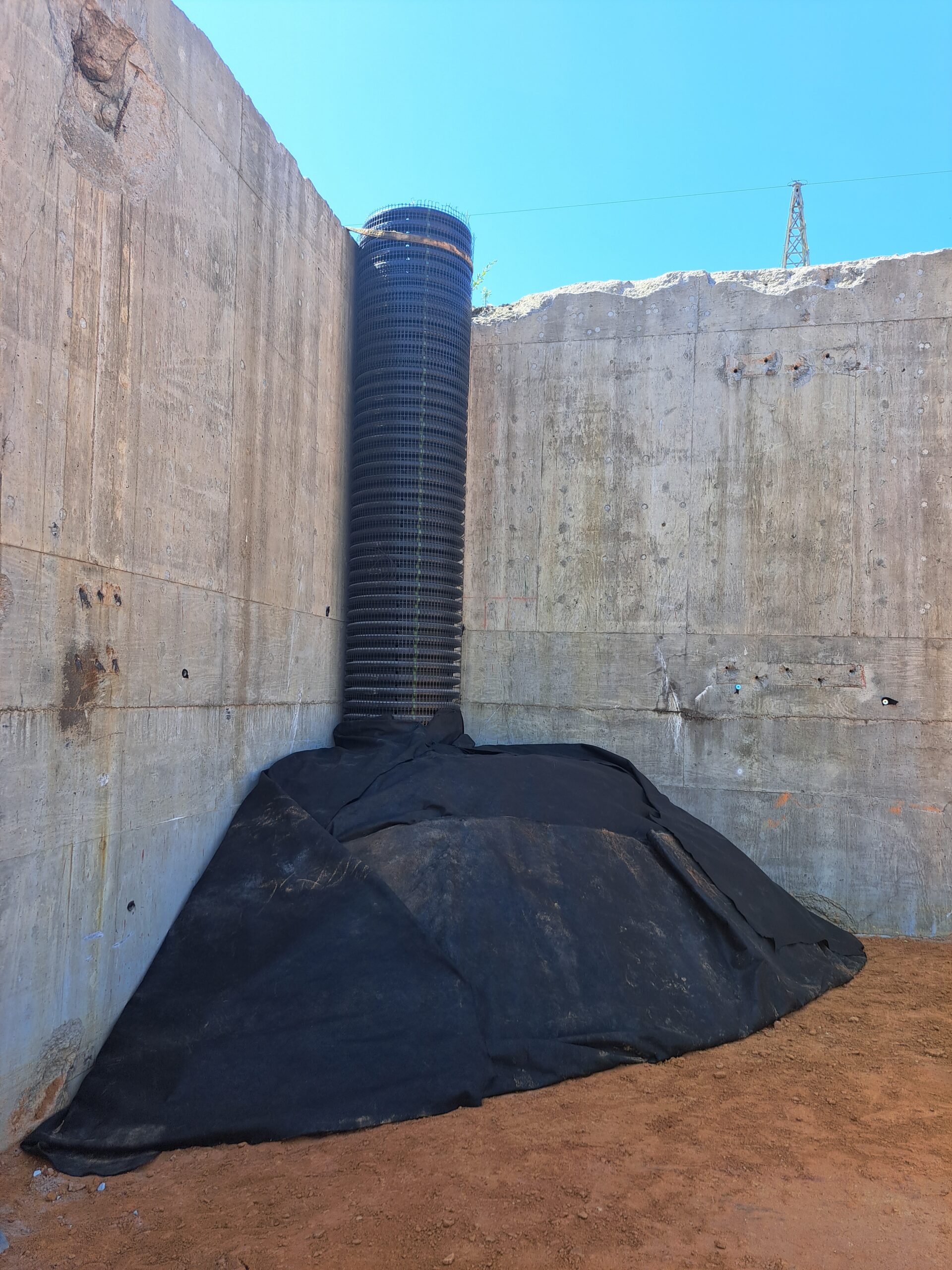
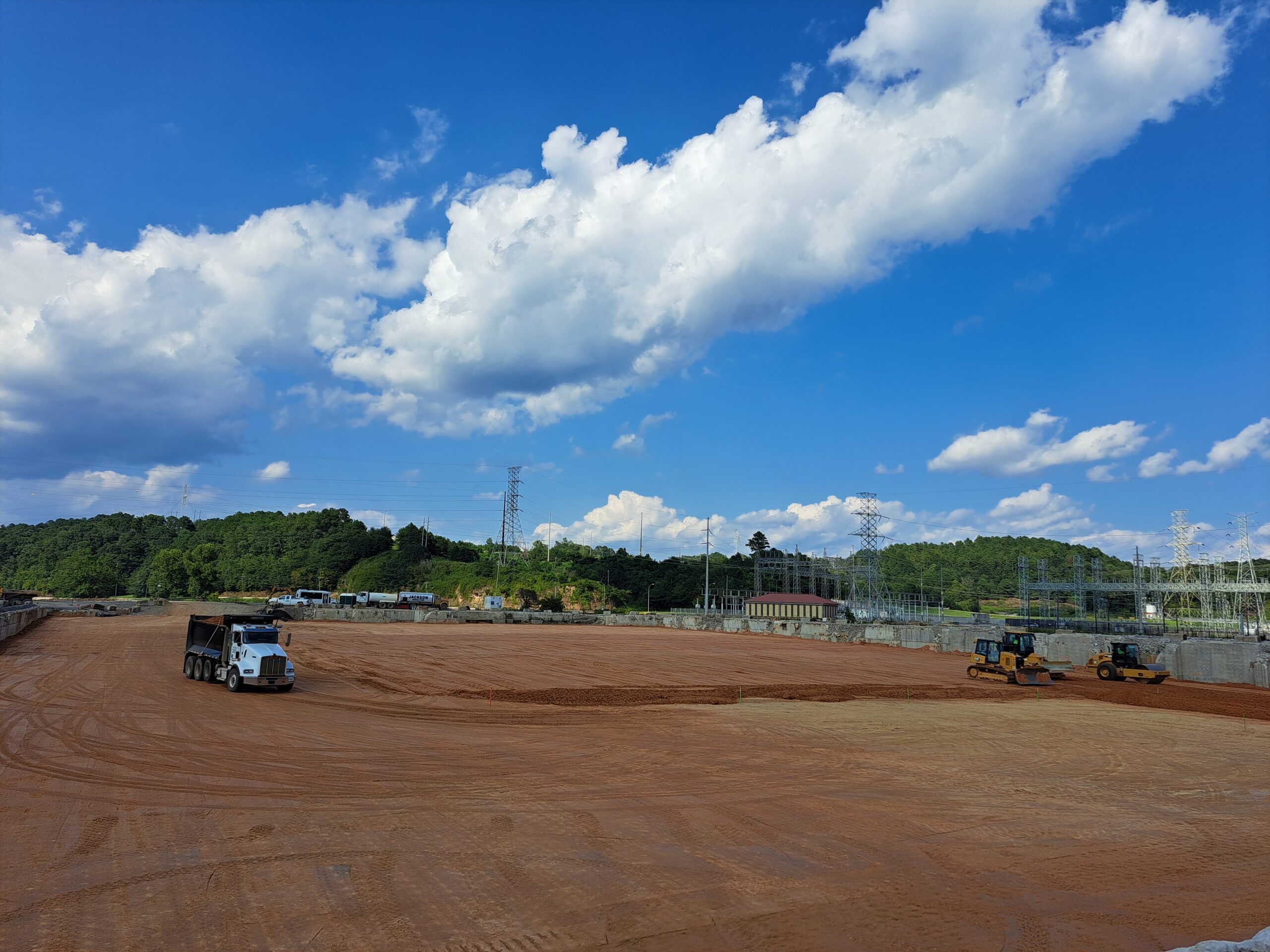
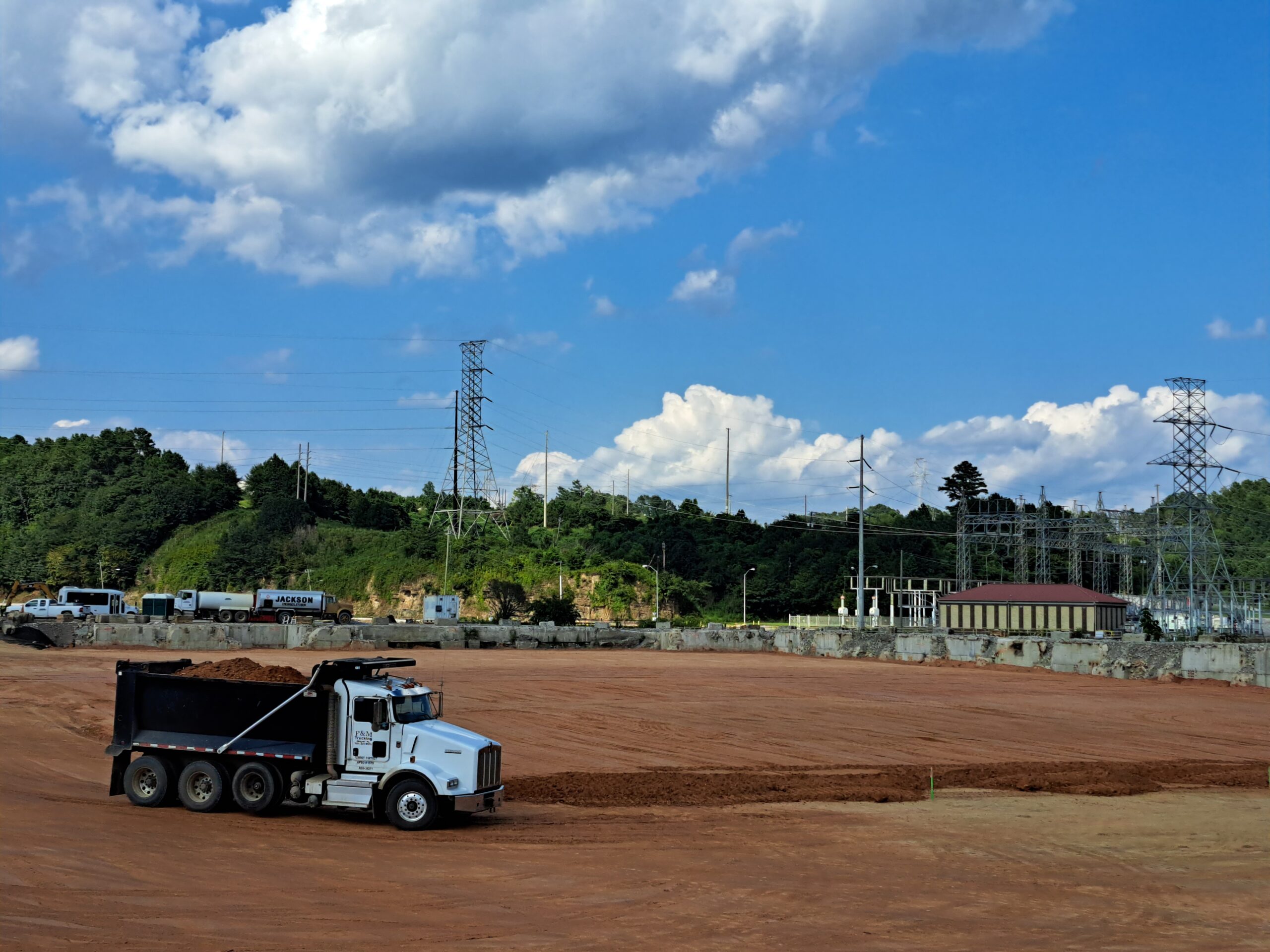
Placement of fill material in section 2 part 1